
روش تولید تختال در فولاد مبارکه
1 – فولاد سازی :
. ناحيه فولادسازي يكي از 5 ناحيه توليدي شركت فولاد مباركه است . وظيفه اصلي اين ناحيه توليد شمش فولادي جهت تأمين ماده اوليه مورد نياز ناحيه نورد گرم به مقدار و كيفيت توافق شده با آن ناحيه توليدي مي باشد .
ناحيه فولادسازي شامل واحدهاي توليدي بشرح ذيل مي باشد :
- واحد حمل مواد Material handling
- واحد كوره هاي قوس الكتريكي Electric arc furnace
- واحد متالورژي ثانويه و آماده سازي پاتيل Ladle furnace treatment and Ladle Total service
- واحد ريخته گري مداوم تختال Continuous Casting of slab
- واحد آماده سازي شمش Slab cooling and conditioning
واحدحمل مواد :
وظيفه واحد حمل مواد تخليه آماده سازي بارگيري ، ذخيره سازي و توزيع كليه مواد اوليه و افزودني فرآيند توليد فولاد در كوره هاي قوس الكتريكي و متالورژي ثانويه مطابق با مشخصات فني تعيين شده مي باشد .
اهم فعاليتهاي قسمت :
- تحويل گيري و ذخيره سازي مواد
- بارگيري مواد در سيلوها جهت مصرف در كوره قوس
- انتقال و توزيع مواد جهت كوره هاي قوس ومتالورژي ثانويه
- بازيافت ضايعات فولادي و آماده سازي آهن قراضه
- كنترل قراردادهاي خريد مواد مستقيم
الف) تحويل و توزيع مواد ورودي توسط نوار نقاله از ناحيه آهن سازي :
به منظور در دسترس بودن مواد و تضمين استمرار توليد آهن اسفنجي و افزودني ها همانند آهك ، دولوميت و…. توسط نوار نقاله از ناحيه آهن سازي به ناحيه فولادسازي منتقل و در سيلوهاي كوره قوس الكتريكي ذخيره مي گردند ، كه اين واحد وظيفه كنترل و زمانبندي عمليات شارژ توسط نوار نقاله ها و انجام عمليات اضطراري تجهيزات مربوطه را بعهده دارد .
ب ) توزيع مواد افزودني و مصرفي با سيستم هاي انبارداري :
دريافت ، انبارداري و توزيع حدود 24 نوع مواد در تناژها ، شكل و اندازه هاي مختلف در نقاط مختلف واحد توليد فولاد نيز توسط اين واحد انجام گرفته وهمچنين در كنترل موجودي مواد مذكور همكاري لازم با قسمتهاي مربوطه نمايد .
ج ) آهن قراضه :
آهن قراضه آماده مصرف پس از تائيد كنترل كيفي – ايمني فني از نظر مشخصات فني توسط تأمين كنندگان با كمپرسي به محل حوضچه هاي ناحيه اعزام و جهت ذخيره سازي در 17 حوضچه مربوطه به ظرفيت تقريبي 45000 تن تخليه مي گردد . سپس باتوجه به دستورالعملهاي مربوطه توسط جرثقيل در سبدهاي مخصوص بارگيري و توسط ماشين حمل به داخل كارگاه جهت شارژ به كوره هاي قوس الكتريكي انتقال داده مي شود .
د ) ضايعات :
با هدف مصرف مجدد ضايعات فولادي ، ضايعات توليد شده در ناحيه با مكانيزمهاي پيش بيني شده به قسمت برش قراضه منتقل و پس از آماده سازي به حوضچه قراضه ها جهت مصرف ارسال مي گردند .
واحد كوره هاي قوس الكتريك :
اين واحد شامل 8 عد كوره قوس الكتريك با ظرفيت توليدي 180 تن فولاد مذاب در هرمرحله توليد باتوان ترانسفورمر 90MVA مي باشد.در ابتدا قراضه بارگيري شده در سبد توسط جرثقيل هاي موجود در اين واحد به داخل كوره قوس تخليه و سپس سقف كوره بسته مي گردد و عمليات ذوب شروع مي گردد . در اين مرحله به كمك قوس الكتريكي قراضه ها ذوب مي گردند به اين مرحلة علميات ( سوراخكاري ) boaring مي گويند سپس شارژ آهن اسفنجي از سيلوهاي ذخيره كوره به داخل شروع مي شود .ميزان قراضه شارژ شده به كوره توسط سبد حدود 40 الي 50 تن مي باشد و ميزان آهن اسفنجي شارژ شده به داخل كوره حدود 170 تن براي هر ذوب مي باشد سرعت شارژ آهن اسفنجي از 500 تا 3200 كيلوگرم در دقيقه با توجه به شرايط ذوب متغير مي باشد . به اين مرحله ذوب (Melting ) مي گويند كه درآن فعاليتهاي زير بصورت همزمان انجام مي شود :
- دمش اكسيژن
- دمش گرافيت
- شارژ آهك و دولوميت جهت توليد سرباره پفكي
- نمونه گيري و اندازه گيري دما
پس از ذوب كامل آهن اسفنجي مورد نياز ، مرحله تصفيه (refining ) صورت مي گيرد و تنظيمات نهايي دما و آناليز با توجه به نتايج آزمايشگاه در اين مرحله صورت مي گيرد و در مواقع لزوم عمليات سرباره گيري از ذوب نيز صورت مي گيرد .
مرحلة آخر در عمليات كوره هاي قوس عمليات تخليه ( Tapping ) مي باشد در اين مرحله پاتيل خالي مذاب كه دماي پيشگرم آن مطابق با دستورالعملهاي توليدي مي باشد به زير كوره هدايت شده و مقادير مورد نياز فروآلياژ و مواد افزودني مانند بوكسيت و آهك همزمان با تخليه مذاب از كوره به داخل پاتيل بارگيري شده و ذوب توليدي در پاتيل مذاب آماده تحويل به واحد بعدي ميگردد. زمان كل ذوب از تخليه ذوب قبلي تا تخليه ذوب بعدي حدود 150 دقيقه به طول مي انجامد و اين عمليات بطور مداوم در اين واحد در جريان مي باشد .
واحد كوره هاي پاتيلي :
اين واحد شامل 4 كوره پاتيلي با توان ترانسفورمر 30MVA مي باشد و هر كوره پاتيلي داراي 6 سيلو (Bin ) با ظرفيت 9 متر مكعب بوده كه موادي چون فرومنگنز كربن بالا و كربن متوسط ، فروسيليسيم ، آهك و كلسيم آلومينات در آنها ذخيره مي گردد .
اهم فعاليتهايي كه بر روي هر ذوب در LF صورت مي گيرد به صورت زير است :
- اكسيژن زدايي
- سرباره سازي
- تنظيم آناليز شيميائي
- تنظيم دما و زمان تحويل به واحد بعدي ( ريخته گري مداوم )
- تصفيه يا حذف آخالهاي موجود در ذوب
اكسيژن زدايي :
جهت حذف اكسيژن محلول در ذوب پس از اندازه گيري ميزان اكسيژن مقدار مورد نياز آلومينيم به ذوب اضافه ميگردد .
سرباره سازي به اهداف زير صورت ميگيرد :
افزايش راندمان حرارتي قوس
- جذب آخالهاي ذوب توسط سرباره
- سولفور زدايي بهتر
- كاهش خوردگي نسوز خط سرباره پاتيل
- جلوگيري از اكسيداسيون مجدد آلومينيم محلول در ذوب
- افزايش بازده و تنظيم راحتتر تنظيم آناليز شيميايي
- تميز بودن پاتيل بعد از تخليه ته پاتيل
- كاهش آلودگي صوتي
تنظيم آناليز شيميائي ذوب :
پس از مراحل بالا و نمونه گيري از مذاب با توجه به آناليز شيميائي دريافت شده مواد مورد نياز به ذوب محاسبه و اضافه مي گردد .
تنظيم دما و زمان تحويل به واحد ريخته گري مداوم :
دماي خروج ذوب از LF بر پايه دماي انجماد نوع فولاد توليدي محاسبه و از طريق سيستم اطلاعاتي به اطلاع اپراتور رسانده مي شود اپراتور جهت افزايش دما بايستي ميزان Tap ولتاژ ترانس ، نوع مواد افزوده شده به ذوب ، ميزان وضعيت سرباره پاتيل ، چگونگي دمش آرگون در پاتيل و…. را مدنظر قرار دهد و پاتيل مذاب را در زمان مناسب كه حدود 20 دقيقه قبل از ريخته گري مي باشد ، از اين واحد خارج نمايد .
تصفيه ذوب :
يكي از وظايف مهم قسمت متالورژي ثانويه حذف ناخالصيها در حد امكان مي باشد و انواع ناخالصيها عبارتند از :
- ناخالصيهاي اكسيدي (MgO , SiO2, Al2O3 و…. )
- ناخالصيهاي كاربيدي ، نيتريدي ، سولفيدي
- ناخالصيهاي فلزي و يا عنصر آلياژي كه بيش از ميزان نياز در ذوب موجود باشد .
- گوگرد و فسفر
- گاز مضر ( هيدروژن ، نيتروژن ، اكسيژن )
واحد ريخته گري :
وظيفه اين واحد تبديل فولاد مذاب به شمش تختال با كيفيت استاندارد ابعاد مورد سفارش مشتري و تحويل آن به واحد خنك سازي و اصلاح شمش مي باشد . اين واحد داراي چهار ماشين ريخته گري دو خطه از نوع قوسي به شعاع 10/5 متر بوده و مشخصات ابعادي محصول توليدي به شرح زير مي باشد :
عرض تختال توليدي : از 650 ميليمتر تا حداكثر 1880 ميليمتر
طول تختال توليدي : در دو نوع تختال بلند 10- 9/5 متر و تختال كوتاه 4/75 – 4/5 متر
ضخامت تختال توليدي 200 ميليمتر
پاتيل مذاب بعد از تنظيم دما و آناليز شيميائي در بخش متالورژي ثانويه توسط جرثقيلهاي سقفي 300 تن به واحد ريخته گري منتقل مي شوند كه هر ذوب داراي يك شمارة 6 رقمي بوده كه كليه اطلاعات ذوب از جمله آناليز شيميايي ، دماها ، زمانها ، كيفيت و … از طريق اين شماره در سيستم MIS قابل رديابي مي باشد در واحد ريخته گري مداوم پاتيل مذاب ابتدا بر روي برج پاتيل گردان قرار مي گيرد وپس از اتصال سيلندرهيدروليكي به دريچه كشوئي پاتيل و تنظيم تانديشكار روي خطوط ريخته گري جريان مذاب از پاتيل به تانديش با بازكردن دريچه كشوئي شروع ميگردد و سپس با بازكردن استوپر جريان مذاب به داخل قالب برقرار مي گردد و با توقف چندين ثانيه اي ذوب در قالب جهت تشكيل پوسته منجمد شده اوليه ، استارت ريخته گري مداوم شروع مي شود و با گذر شمش تشكيل يافته در قالب و در ادامه از مابين غلتكهاي همراه با پاشش آب بر روي سطوح آنها جبهة انجماد در داخل شمش رشد نموده و در نهايت با رسيدن شمش به طول متالورژيكي ، بطور كامل در سطح مقطع تختال انجماد حاصل مي شود و در ادامه با رسيدن
شمش به قسمت برش طول تختال و با در نظر گرفتن حداقل ضايعات در انتهاي ريخته گري برش داده مي شود و پس از خروج تختال از ماشين برش بوسيلة ماشين شماره زني يك شماره 9 رقمي جهت شناسايي و قابل رديابي بودن تختال بر روي آن حك مي گردد .
با پايان ذوب اول ، ذوب دوم كه بر روي بازوي ديگر برج پاتيل گردان قرار دارد گردانده شده و بر روي تانديش قرار ميگيرد و بلافاصله پاتيل باز مي شود تا تداوم و پيوستگي ريخته گري حفظ شود . ذوبهاي متوالي بطور متوسط حدود بيش از 5 ذوب در يك عمليات به شمش تختال تبديل شده و تختالهاي توليدي جهت خنك سازي واصلاح به واحد بعدي تحويل داده مي شوند .
واحد خنك سازي واصلاح شمش :
در اين واحد به دو صورت و براساس نوع تختال توليدي خنك سازي صورت ميگيرد :
- خنك سازي با هوا
- خنك سازي با آب
تختال هايي كه براساس كيفيت نياز به خنك سازي با هوا دارند توسط جرثقيل هاي سقفي به قسمت مربوطه منتقل و پس از گذشت 72 ساعت تختال خنك شده به قسمت اصلاح تختال ارسال ميگردد .
تختال هايي كه نياز به خنك سازي آب دارند توسط ميز غلطكي هاي موجود به دو تانك خنك سازي انتقال داده شده و توسط دو جرثقيل به صورت اتوماتيك به داخل تانك شارژ شده و تختال خنك شده (پس از حداقل20دقيقه ) از تانك خارج و به قسمت اصلاح تختال ارسال ميگردد .
در قسمت اصلاح تختال ، تختالها توسط بازرسين كنترل كيفي بررسي و در صورت وجود عيوب سطحي آنها را مشخص مي نمايند سپس اپراتورهاي واحد اسكارف توسط مشعلهاي دستي اين عيوب را برطرف مي نمايند و پس از تائيد نهايي واحد كنترل كيفي تختالها به ناحيه نورد گرم انتقال داده مي شوند ولي در صورت عدم تطابق با برنامه پذيرش ناحيه نورد گرم تختالها در انبار نگهداري و به تدريج به ناحيه نوردگرم فرستاده مي شوند .
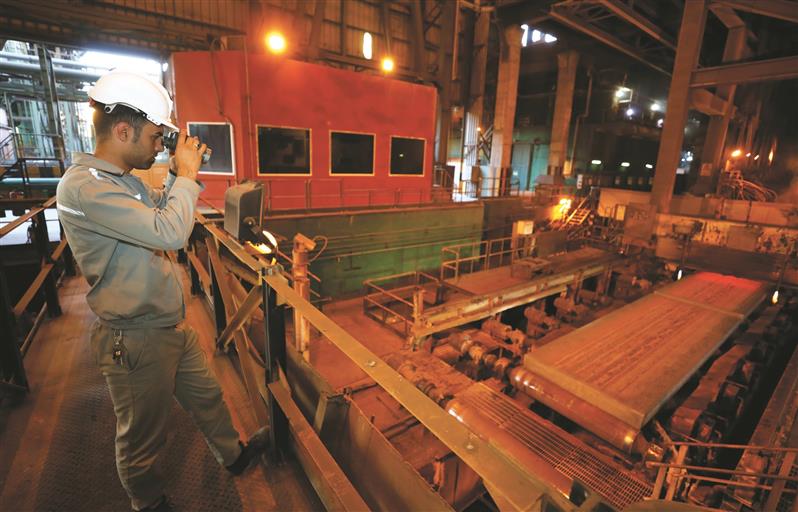
2 – نورد گرم فولاد مبارکه :
تختالها به واحد نورد گرم منتقل مي شود و پس از گرم شدن تا 1280 درجه سانتي گراد در كوره هاي پيش گرم كن و پوسته زدايي در نورد هاي اوليه و نهايي نورد شده و در نهايت ضخامت آن به 16 تا 1/2ميلي متر مي رسد كه به صورت كلاف ( كويل ) توليد مي گردد .
کلاف گرم با مشخصات ابعادی :
- ضخامت از 1/5تا 16 ميليمتر
- عرض از 650 تا 1850 ميليمتر
- وزن بسته بندي محصولات از 5 تا 30 تن
جنس کليه محصولات ساختماني و فولادهاي ويژه ذکر شده در دفترچه مشخصات موجود مي باشد.
کيفيت سطح : فولاد سياه با صافي سطح کمتر از IU-85
واحد تکميل نورد گرم :
52درصد از كلافها به واحد تكميل نورد گرم انتقال مي يابد . در اين واحد اعمالي از قبيل كم كردن وزن كلاف ، بهبود خواص مكانيكي ، تسطيح ورق ، برش سبک و سنگين ورق در طولهاي 1 الي 12 متر صورت مي گيرد .
محصولات :
کلاف و شيت
- کلاف مانند مشخصات فوق — فولاد سياه با سطح (Flatness) کمتر از IU-20
- شيت حداکثر طول 1 تا 12 متر — وزن متفاوت مطابق با سفارش مشتري
ضخامت : 1/5 تا 16 ميليمتر
خدمات بر روی ورق :
جهت تولید محصولات فولادی در مواقعی نیازمند تبدیل کلاف به عرض های کمتر می باشیم در این هنگام از روش نواربر کلاف مادر به چند کلاف با عرص های در خواستی تبدیل می گردد.
نواربر یا اسلیت :
این خط کامل جهت تبدیل کلاف های فولادی به نوارهای فولادی کلاف شده از ضخامت 1 تا 10 میلیمتر مورد استفاده قرار می گیرد.کویل گیر این خط 25 تنی می باشد و ورق هایی تا عرض 1600 میلیمتر را به نوارهای فولادی تبدیل می نماید.